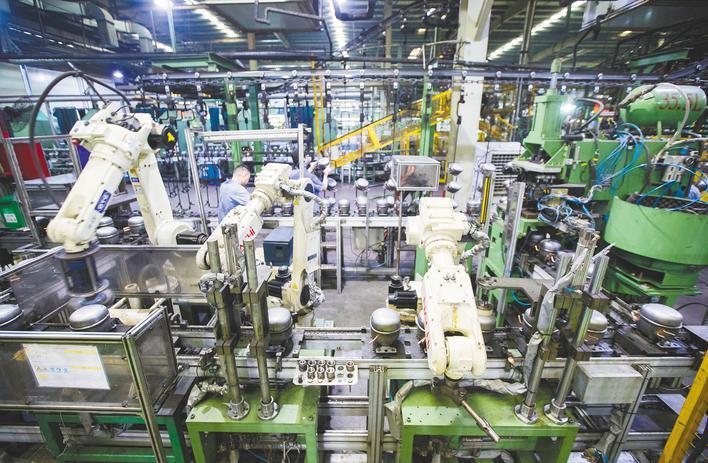
開發區·鐵山區
生產線上的固定安裝程序,一雙雙機械臂嚴絲合縫地完成,并且隨時待崗待命;零配件的質量是否合格,一雙雙“透視眼”隨時監控;新訂單什么時候做、要做多久、配料是否足夠,一套新的“智慧大腦”會進行最合理的安排配置……
走進湖北東貝機電集團股份有限公司(以下簡稱“東貝集團”)生產車間,“人機”配合的智能化生產線,標志著企業從傳統制造向智能制造的全新蛻變。
生產線上的“新員工”
作為一家老牌的制冷壓縮機生產企業,從2018年開始,東貝集團大力推進技改,提升產線自動化水平。
經過5年的科技創新,如今忙碌在東貝集團生產線上的,除了專業的工作人員,還有靈活的工業機器人。
在東貝集團的殼體車間,生產線采用“舊設備+工業機器人”的方式進行整體布局,在其中一道生產工序中,橙紅色的“機器人”把守著6個特殊的專屬工位,只要接到指令,便會不斷伸出“手臂”,完成操作工序。
“這種局部自動化、半自動化搭配的方式,極大提升了生產效率和靈活性。”東貝集團壓縮機公司智能辦副部長錢俊介紹說,以前一條生產線上需要6—8名工人,有了工業機器人的協助,2名工人可以操控一條生產線。
在裝配車間里,生產線上裝載了集成視覺系統,這些“透視眼”可以對每一個產品進行高精度拍攝,實現“即時生產、即時檢測”,并自動保存數據傳輸至數據庫,為精準操作、精益運行提供依據和支撐。
據介紹,自2019年以來,東貝集團陸續引進工業機器人約400臺,推進自動化項目300余項,標桿場景自動化率超80%。
看不見的“智慧大腦”
從優化產線與產品匹配,再到以工業機器人、機器視覺為突破口,實施單點自動化試點,最終串聯多臺自動化設備,實現自動化連線的智能工廠,東貝集團的生產線逐漸建立起一個看不見的“新大腦”。
自2022年起,東貝集團全面加速數字化轉型,引進先進管理系統,逐步貫通生產、銷售、設計環節,形成縱向互聯、橫向互通的數字化生態,打造出全價值鏈協同的一體化信息平臺,實施了700余項變革。
歷經近兩年打造,數字化平臺初具規模。CRM、APS、SRM、MES等系統各司其職,從訂單管理、生產計劃優化、供應鏈透明化到生產過程監控與質量追溯,實現了產供銷的無縫對接與高效協同。
“我們對海爾、海信等重點客戶開放了后臺權限,客戶可隨時查看生產進度、批次、質量等。”錢俊表示,這種管理方式使得產品追溯更加便捷,也進一步提升了生產管理的精細化水平。
以前,新訂單來了,什么時候生產、需要多少原料等信息,都靠人工排期,往往容易出現缺少原料等情況。如今,新的管理系統能夠對訂單進行智能排期,讓工廠里的生產最優化、有條不紊地進行。
如今,自動化、數字化、智能化轉型,助力東貝集團生產效率躍升40%,標桿產線產量從原來的日產1萬臺,提升至日產1.4萬臺,質量合格率也提升了25%,持續引領行業變革。
(選自 湖北日報客戶端開發區·鐵山區頻道 作者 曾麗妮 胡靖 嚴逸亭)
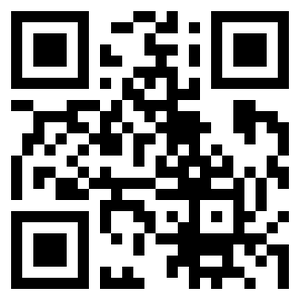
VIP課程推薦
APP專享直播
熱門推薦
收起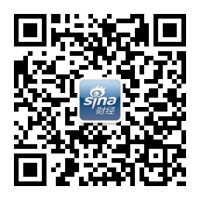
24小時滾動播報最新的財經資訊和視頻,更多粉絲福利掃描二維碼關注(sinafinance)